Quicker Compaction
By Paolo Benedetti
On many pool projects, the excavation phase often calls for the addition of competent fill to establish a foundation solid enough to support a concrete structure. That extra step can be both laborious and expensive, observes watershaper Paolo Benedetti, who uses this fresh entry in his new series on sensible solutions to common technical problems to describe a time- and money-saving alternative to standard methods of soil remediation.
Without exception, you must be certain you’re building your watershapes in competent soil. That’s why in my firm’s work – as designers, as builders and even as consultants – we require a geotechnical investigation for every project in which we become involved.
Trouble is, even with capable site analysis, you’ll sometimes run into surprises: Although geotechnical engineers carefully select where to bore holes in the areas where pools, spas or fountains are to be built, these sample points result only in generalizations about a site’s conditions. Oftentimes during excavation, in fact, we’ll encounter conditions that are much worse than reports would have led us to expect.
For the most part, these variances have to do with unexpected thickness or unpredictable distribution of ground deposits, and they can occur whether we’re working in rock, clay or loose fill materials. Typically, geotechnical engineers will ask us to remove the incompetent material and replace it with newly compacted fill – a laborious process to which we’ve found an acceptable alternative.
A QUICKER FIX
Standard removal and refilling requires all the labor involved in excavating and carrying away the “bad” material, bringing in “good” material and then compacting the new material – a process that requires constant inspection by geotechnical engineers to verify that everything has been done properly, layer by layer.
After we’d removed an undesirable layer of expansive clay material, the shallow end of this pool became too deep for the planned beach entry. To remedy the situation, we placed a six-inch layer of drain rock and created terraces with gravel-filled bags intended to retain an engineered fill.
This isn’t something that makes anyone happy – except maybe the engineers, who are paid for their time but still must endure the tedium. For the most part, it’s a woeful redirection of effort that throws contractors off schedule and is invariably an expense that homeowners haven’t anticipated.
In recent years, I’m happy to say, we’ve found a different approach that’s faster, easier and more economical.
When we encounter incompetent material in the excavation phase, we complete the work as though nothing was wrong. At that point, with the site fully exposed, we bring in the geotechnical engineer for what is often referred to as a “bottom inspection.” The purpose of this visit is to determine the depth or thickness of the incompetent materials.
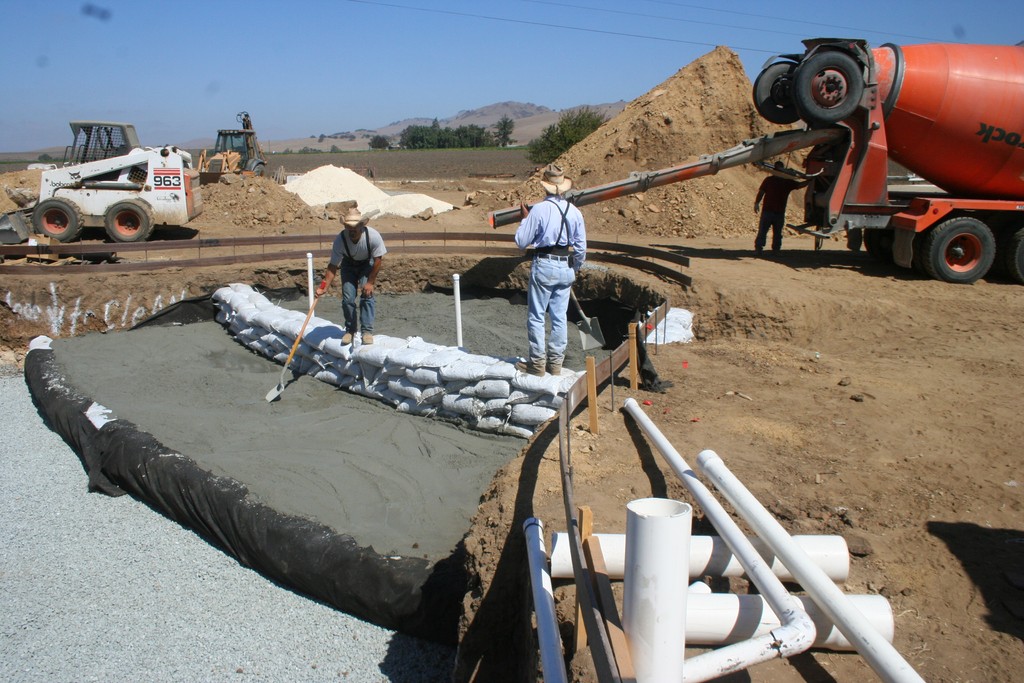
If it is determined that the materials are not too extensive (say, three to six feet deep), we move forward and over-excavate to get rid of the garbage. We then prepare the site for importation of “engineered fill” – a slurry/grout mix containing 3/8-inch rock.
In doing so, we place all required plumbing that will stub up in the area, creating shallow trenches in the competent soil and covering them with sand. We then wrap the vertical risers in a half-inch of foam (or newspaper bound in duct tape) to ensure maintenance of voids in the engineered fill.
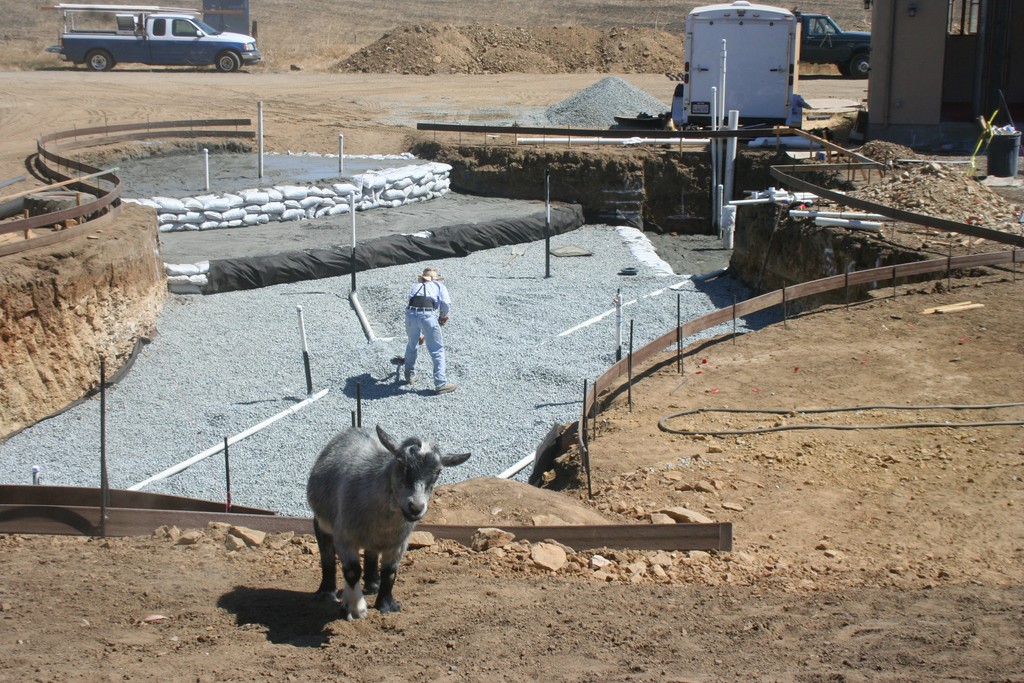
The fill’s mix design includes water-reducing admixtures, so even though the slurry seems fluid and self-consolidating, it actually contains very little water. To control its flow, we stack gravel-filled sandbags to serve as berms – in sloping areas of the excavation, for example – that contain the mix at various elevations. We then place the fill up to the level of our initial “rough excavation” before vibrating it into place.
This becomes the competent base atop which we place our reinforcing steel. From that point on, construction proceeds as usual.
This is a much simpler approach to soil remediation than standard compaction – one we’ve also used with structural-concrete mix designs, for example, in creating “deepened foundations” for hillside pools where we’ve needed to build up an earthen substrate to the desired elevation for pool construction.
This is a terrific solution in appropriate situations: It doesn’t push geotechnical engineers out of the picture by any means (after all, they still must inspect the excavation and approve the use of engineered fill), but it considerably speeds the process in ways that save my clients money and helps me keep projects right on track.