Pool & Spa News Online - Coverups Lowering the Skimmer
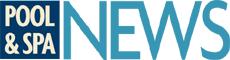
Coverups Masonry Lid Variations
This method saves water - and looks great.
By Paul Benedetti August 2003
Special to Pool & Spa News

Variation I
I had one project where a planter pushed right up to the back of the box. The coping material was 24 inches wide, so it spanned the dam and the trays. But it left the back wall of the cover box exposed, so we had a 6-inch gap between the trays and the planter. We had used flagstone on the deck, but the homeowner didn’t want to cover the wall with 6-inch pieces of flagstone because it would look contrived.
We did put a single course of flagstone pieces on the wall, but the pieces varied in size: Some pieces measured as large as 3 feet. We cut one side of the stones to be flush with the back of the trays, then let the rest cantilever into the planter. So there was an irregular stone pattern jutting into the planter.
We couldn’t just cantilever this much stone over the wall and expect it to support people walking on it. So we doweled the overhang into the back of the cover-box wall and poured a little footing underneath each stone.
This zigzagging edge softens the transition to the planter, gives us a wider walkway and eliminates the little visual 6-inch strip.
Variation II
A project we’re working on now requires an extra large cover box: 3 feet wide with 12-inch walls, compared with the normal 18-inch box with 6-inch walls.
Of course, I still wanted to cover the box with masonry — flagstone, in this case. But the regular masonry brackets couldn’t support the 300 to 400 pounds of stone necessary to cover the box.
I spoke with our cover company’s engineer, who said we could support the material with a 4-by-4-inch stainless steel beam spanning the width of the box.



The beam had to go right over the cover dam. So now we’d have this ugly steel beam in full view. My cover manufacturer suggested covering the front, visible part of the beam with the same green glass mosaic tile that we were using at the waterline. That tile would cover the top of the dam wall, as well. This way, the green on both surfaces — the front of the steel beam and the top of the dam wall — could blend together once under water. (This dam wall would be submerged because the cover box with these covers stay flooded.)
We didn’t think the mortar would adhere to the flat stainless steel surface, so we had the beam covered with an expanded stainless steel mesh. To help support the tile and serve as a guide line, a small stainless steel ledge was welded to the bottom of the beam face. The ledge stuck out about 1/2-inch.
The toughest part was installing the beam. Stainless steel is such a tough material that we couldn’t hand-drill it on site to bolt onto the structure. The beam had to be drilled in a machine shop with oil-cooled drill presses, making it impossible to build it into the wall during gunite. To get the bolt holes just right in the structure, we used the beam as our template.
We started with a 4-by-4-inch notch in the gunite on either side of the cover box. The beam would fit in place in the notches. We needed to attach the beam with one bolt in each notch. A hole was drilled in the bottom of each notch. We oversized the holes so we’d have a little bit of wiggle room.
Then we literally bolted the bolt onto the beam, shot the epoxy in the holes at each end and lowered the beam down — with the bolt sticking out of the bottom — until the bolts fit into the holes in the pool walls. After the epoxy set up (about 15 minutes), the beam was unbolted and lifted off the bolts. We wanted to let the bolts sit for a couple of days before permanently installing and leveling the beam. Finally, we spread a little bed of mortar on the bottom of each notch, reinstalled the beam and leveled it while the mortar was still wet. A bead of epoxy was laid where the beam met the gunite, then bonded it with bonding wire on both ends.
The tile crews did their job, starting at the bottom of the beam where the ledge sticks out and working their way up.
From a distance, it now appears that you’ve got a tile waterline all the way around the pool. The effect will be even more complete when the pool is filled with water.
Paul Benedetti is vice president of Aquatic Technology Pool & Spa in Morgan Hill, Calif. The former service technician now specializes in the design and construction of high-end aquascapes. He has taught courses about intricate aquascape design and is an associate member of Genesis 3. Benedetti is a subject-matter expert for the state of California and assisted in writing California’s most recent pool contractor’s examination.
© 2003, Pool & Spa News