Avoiding Electrical Missteps
By Paolo Benedetti
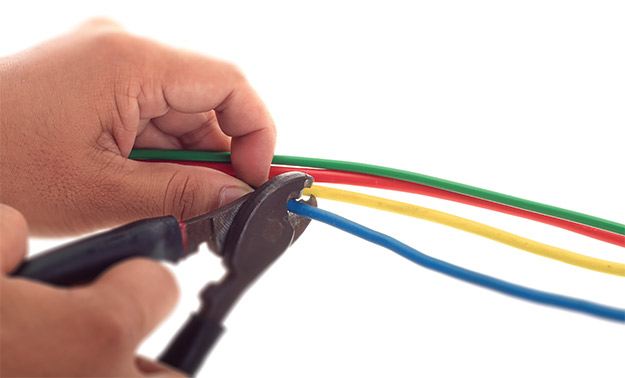
Electrical safety in swimming pools and spas is governed by Article 680 of the National Electric Code along with a number of other sections of the code. Because the requirements are complex and ever changing, complying with the letter of the standard can be challenging. Here expert builder Paolo Benedetti shares a number of requirements that are commonly missed, even by the most conscientious of builders.
The National Electric Code is scrupulously written to provide clear requirements for ensuring bather safety. As sturdy as the NEC may be, however, it does little good if its requirements are not followed, which has recently led to electrocutions and tragedy. Here, experienced builder Paolo Benedetti of Aquatic Technology Pool and Spa offers a list of common mistakes he's seen in the field and the remedies needed to bring pools into code compliance.
When you follow incidents involving electrocutions in swimming pools, in almost each case there's some form of violation of the National Electric Code. It's a terrible subject, but one we must take up just as we have addressed industry standards for hydraulic safety.
The good news is that electrocutions are relatively rare. This is precisely because NEC Article 680, in addition to a handful of other sections in the code, requires measures that when followed to the letter have been proven to protect bathers. The problem is that even experienced builders will sometimes miss the mark on specific requirements.
In my long career building and renovating pools, I've had countless opportunities to inspect a wide spectrum of installations. Oftentimes, I've been surprised to find many instances where, for whatever reason, the systems are not in full NEC compliance. Knowing full well that no one in our industry wants to see any one injured (or worse) in one of their pools, it's my personal belief that the vast majority of these mistakes are due to a lack of understanding of some of the finer points in the code.
To be clear, however, regardless of some of the nuances in the NEC, ignorance is no excuse. That's why I've made it my business to become as well versed has possible in all of these crucial, potentially life-saving measures. I've based the following list on my own reading of the NEC and the most common types of mistakes I've seen over the years. My hope is that reading this list will help builders avoid similar dangers, and also prompt everyone in pool construction to take a closer look at the all the applicable sections of the NEC for the specific language.
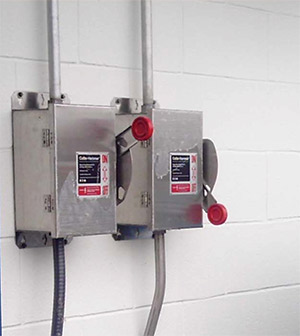
EQUIPMENT GROUNDING [NEC 680.25(B)]
This is a common mistake, one that I used to make until about 10 years ago when I discovered the error of my practice.
When builders set up outlet boxes, they go to Home Depot and buy either a single-gang or double-gang aluminum box. They run power into one of the holes and then use the others to connect flexible conduits for AC wiring to pumps, heaters, etc. (I've also seen plastic boxes or wire gutter for the same purpose.). They'll run a bunch of wires through the flex conduits into the box and connect the ground wires with a simple wire nut, which is fine anywhere else in the home, but not around a swimming pool (or any other body of water).
According to the NEC, all grounding connections have to be made using a ground bar, the kind where you back off a setscrew, insert the wire into a hole in the bar and tighten it back down. You're pinching the wire firmly into the bar. The reason being if someone inadvertently pulls on the wire somehow, there's a chance that the wire will come loose from a wire nut, and all of a sudden you'll have an ungrounded piece of equipment, and that presents a hazard.
The grounding bar — the same thing you'll see in a service panel — is an aluminum bar with a bunch of holes and screws that is used to make a firm connection. It's written in the code because the idea is to create a permanent connection that won't come undone.
So when you're using one of these outlet boxes, you need to install a grounding bar into it, which costs almost nothing and takes only a few minutes. Since electrical boxes are not made specifically for pools and don't come with grounding bars, it's up to the builder — or more to the point, the electrician — to install the grounding bar in the box.
By contrast, if you look at a pool light junction box, there's a terminal bar inside, precisely because manufacturers know the NEC requires a permanent, non-corruptible connection for ground wires. Even pump motors have a single terminal screw for the ground wire connection.
REDUNDENT BONDING (NEC 680.24(F), 680.26(B)(6), 680.6)
On a related note: There's a big trend right now toward the use of LED lights, which do not require a ground, but the wiring still must terminate above water level in a junction box. And those boxes still need to be bonded and grounded.
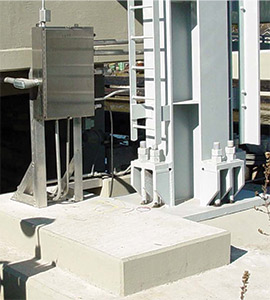
Builders typically use the same style of junction boxes they used to use for high-voltage lights, meaning the boxes have a grounding bar, which still needs a bonding and grounding connection. The reason being, someone might come along and install a high voltage light in the same fixture and could easily forget about bonding the junction box, which as we know could then lead to unequal electrical potential.
Though LED lights themselves do not require bonding (NEC 680.33), you still need a stranded number 8 copper wire coming from the equipment pad through the conduit into the box, and a solid number 8 wire outside the box connecting to the deck or pool steel. That makes the junction box safe if someone comes along after you and changes the lighting system. Sections NEC 680.6(4), 680.25 (D) & (F), specifically state that junction boxes shall be grounded. At this time, the NEC does not differentiate if the junction box is being utilized for high or low voltage connections in regards to bonding and grounding.
Like many builders, I use pool light junction boxes for all sorts of things — not only high and low voltage lighting but also for sump pumps or underwater speakers. The bottom line is anytime you're using something that has a bonding connection, you have to be sure it's bonded. Otherwise, you can create a situation that is a potential hazard.
I've seen the same thing in equipment rooms. You'll have a control panel, for example, and on the inside it has all the grounding and bonding wires attached inside, but on the outside of the box is the copper lug where you're supposed attach the bare copper bonding wire and run it down to the equipment pad's reinforcing steel and bonding grid. All too often I've seen installations where that lug is just sitting there unused. Presumably, the installer assumes that connections inside the box are adequate, but things happen that can corrupt those connections, which is why the NEC calls for the redundant bonding.
Keep in mind, we're only talking about a few dollars in wire and a small amount of labor. You're already pulling wires through the conduit anyway, so it's really no big deal to pull in the stranded wire from the equipment pad. Likewise, running the bare bonding wire from boxes to structural steel is not labor intensive. Think of it as extremely inexpensive insurance, because you never know what someone is going to do to the system after you've gone.
And keep in mind that anyone who has ever touched the system still owns it in terms of liability. So ground and bond the boxes, even if they're being used for LEDs or low voltage connections.
JUNCTION BOX ELEVATIONS (NEC 680.24)
This is another simple measure, but one that seems to cause some confusion. The NEC calls for installing lighting junction boxes four inches above the "maximum" water line. That doesn't mean four inches above the ground and 8 inches above the maximum operating waterline (meaning the water level you would have if the pool overflows).
Depending on the pool design, that difference could be anywhere from 4 to 8 inches or more.
The mental disconnect on this requirement comes into play when a builder assumes the overflow line represents the maximum waterline, which most the time it is, unless that line becomes plugged somewhere. Therefore you should never assume that just because you have an overflow line, there's no chance the pool will ever overflow.
The point of this requirement is simply to avoid water backing up in the conduit and entering the junction box where the electrical connections are housed. The NEC authors have determined that elevating the box 8 inches above the highest possible waterline will prevent that, even when an entire little league team jumps in the pool at the same time creating bather surge, causing the water in the conduit to bob up and down.
EQUIPMENT & DRAINAGE (NEC 680.11)
Paraphrasing the NEC, equipment for pools, spas, hot tubs, fountains, etc. shall not be located in areas that lack drainage for water that might accumulate during normal system operation or filter maintenance. In other words, put drains in your equipment pads so no one ever has to work on the electrical equipment while standing in water.
A lesser-known requirement in a separate section of the NEX says equipment shall not be located in a room where water is able to spread across the room to the electrical panel. Again, the idea is to prevent a situation where someone is standing in water while turning off electrical breakers.
To meet that requirement, you can either build a curb around the equipment for containment or build a raised section of the equipment room floor right in front of the electrical panel in case something starts to leak and the gravity drain is blocked.
In addition, another related (and commonly missed) requirement involves elevating the equipment off the floor so that if the room floods above a secondary drainage path, usually under the equipment room door, water cannot rise up and come in contact with the equipment.
The tricky thing about that requirement is that it depends on the installation. If, for example, you have an equipment room or pad that requires you to step down two steps to enter the room, the equipment should be raised above the potential water level on 8-inch to 12-inch blocks. I have found that square CMU column blocks filled with concrete make excellent poured-in-place forms. At a minimum these "housekeeping" blocks should be 6 inches high and 6 inches wider than the equipment they support.
A sump pump typically provides flood protection for subterranean equipment rooms. But we all know that sump pumps fail, and it's impossible to raise the equipment high enough. That's why a water level sensor alarm should be employed as an inexpensive back up. It is wise to provide personnel with a warning before they step into a room full of water.
Even in those situations, I still take the added step of elevating equipment off the floor, just as an added measure against water reaching the equipment and potentially energizing the water.
CLEARANCES (NEC 110.26)
Another related measure involves clearances for electrical panels, meaning you must have clearances 30 inches wide, 36 inches in front and 6 feet of headroom. In other words, set up the equipment area so that somebody working at the panel will not inadvertently come in contact with something that can cause them to become the path to ground.
Of course, many equipment rooms are so crowded that it's tough to find that much room. All too often, the panel is on the wall at the back of the pad where someone has to climb over the equipment to get to it. Unfortunately, that creates a hazard. There's usually no reason you can't mount the panel at the front of equipment area or on a post somewhere, but wherever it is, per the code, it's necessary to design the space with adequate clearance in mind.
SERVICE DISCONNECTION (NEC 680.12)
The code requires a permanent means of disconnecting equipment for service purposes located on the equipment itself or within the line of sight of the equipment.
According to the NEC, breakers shall not be used as the disconnection means for motors greater than ½ horsepower [NEC 430.109(B)], presumably because they can wear out over time. For motors between ½ and 2 horsepower, you cannot rely on the breaker and need a separate switch [NEC 430.109(C)] to disconnect the power.
I've run into issues with variable speed pumps because they are wired to have live power running to them 24/7. They're turned on and off via a data cable and not by way of a power switch. As is, the only way to turn off the power to a variable speed pump is at the circuit breaker.
The solution is to install an approved disconnection switch in the line between the circuit breaker panel and the equipment.
GFCI MOTOR PROTECTION [NEC 680.21(C)]
Since 2008, the NEC has required GFCI protection of all pumps that operate on single phase, 120 through 240 volts, rated 15 or 20 amperes. This is required whether the pump is hard wired with conduit or plugged into an outlet with a locking cord. This is clearly explained in the NEC 680.21(C) Handbook narrative.
Pumps that operate on three phase, voltages greater than 240 or when rated above 20 amperes do not require GFCI protection. These phase, voltage and amperage criteria are based upon the motor data plate ratings.
FLEX CONDUIT (Liquid Tight Non-Metallic Conduit – LNMC, NEC 356.10)
Let's sign off with a really simple one, but again, an issue that is commonly missed.
The code limits the length of flex conduit to 6 feet [NEC Section 356.12(3)] because it wears out and is generally more susceptible to damage than rigid conduit. Yet time and time again I've seen installations where the flexible conduit is run all over the equipment pad, presumably because the installer doesn't want to go to the effort of mounting rigid conduit and then switch to flex for the last few feet.
Whatever the reason, we all need to follow the rules and limit our use of flexible conduit per the NEC.
And, really, that same thing applies to all the rules in the NEC. Be familiar with the requirements and follow the rules. In doing so, we might someday reach the only acceptable number of electrocutions — zero!